April 12, 2023
Small steps go a long way to prevent damage claims
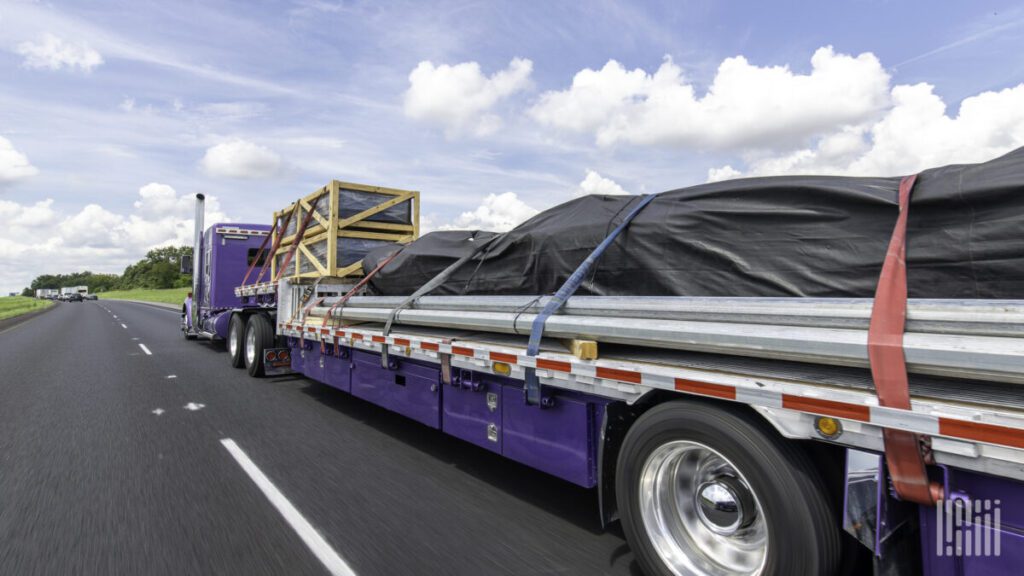
Reliance Partners shares essential tips for drivers and carriers
Shippers and carriers alike probably agree that one of their highest priorities is for shipments to arrive damage free.
Achieving this is the driver’s and carrier’s shared responsibility, and often it goes off without a hitch. But due to countless controllable and uncontrollable variables, shipments don’t always arrive in the condition listed on the bill of lading.
Unless carriers can prove any inconsistencies with the BOL compared with delivered freight were the fault of the shipper, which is a tough position to be in, carriers are often liable. Shippers and receivers can file a few different types of freight damage claims to recoup the lost value of their products, including concealed damage, visible damage, shortage or loss.
As freight claims can quickly become a steep expense, depending on the goods involved, it’s no surprise that carriers protect themselves with cargo insurance to help offset claim costs.
“There’s always an opportunity for a claim,” said Robert Kaferle, vice president of safety at Reliance Partners, a trucking insurance agency and safety consultant. “Cargo insurance doesn’t cost that much, but covering yourself and your company is paramount.”
While insurance is essential protection for carriers, preventing damages in the first place is always necessary to avoid any cash payouts and maintain trust with shippers and customers.
Small steps can go a long way to avoid damage, and drivers play a frontline role in this.
Preventing damage claims
Freight damage can occur due to factors both in and out of drivers’ control, so upon pickup, they must do their due diligence to ensure cargo is stacked, wrapped and secured properly in accordance with the procedures for the type of goods and trailer.
“Take advantage of that opportunity to inspect the load to make any changes or load securement suggestions,” Kaferle advised. “Ultimately, the driver is going to be responsible for the load in their care, so it’s up to them to make sure it’s good to go.”
In a lot of cases, loads may already be sealed before a driver arrives at the loading dock. Kaferle still recommends drivers take steps to do a quality check where possible.
“Even when it’s preloaded, there’s some responsibility that will fall on the driver,” Kaferle added. “Train your drivers to make sure the load is documented correctly, look at anything unusual on the BOL and then ask questions. A load can always be resealed, so if there’s ever any doubt about how it was loaded, or it appears to be leaning or bulging, always have the seal broken before you take the shipment.”
That documentation step is key. Drivers should verify BOL load counts always match actual cargo, notate any existing damages and include whether they couldn’t witness loading.
Visual proof is essential to confirm whether damage occurred before it was picked up by the carrier.
“Drivers should take pictures of how the trailer is loaded upon pickup and at the destination as well,” Kaferle advised. “Everyone’s got a cellphone and camera, so there’s no excuse not to take photos.”
Ultimately, driver training and awareness of cargo securement and BOL documentation are critical. Kaferle recommends carriers provide drivers with continuous training for these practices throughout their employment, not just during orientation.
“There’s always something to learn or reiterate, so it doesn’t matter how long you’ve been in trucking,” Kaferle said.
Reliance Partners provides its clients with driver training resources in skills like cargo securement and many other key safety requirements in order to help them build a more compliant and thorough safety program.