June 24, 2022
In the trucking industry, saving pennies can add up
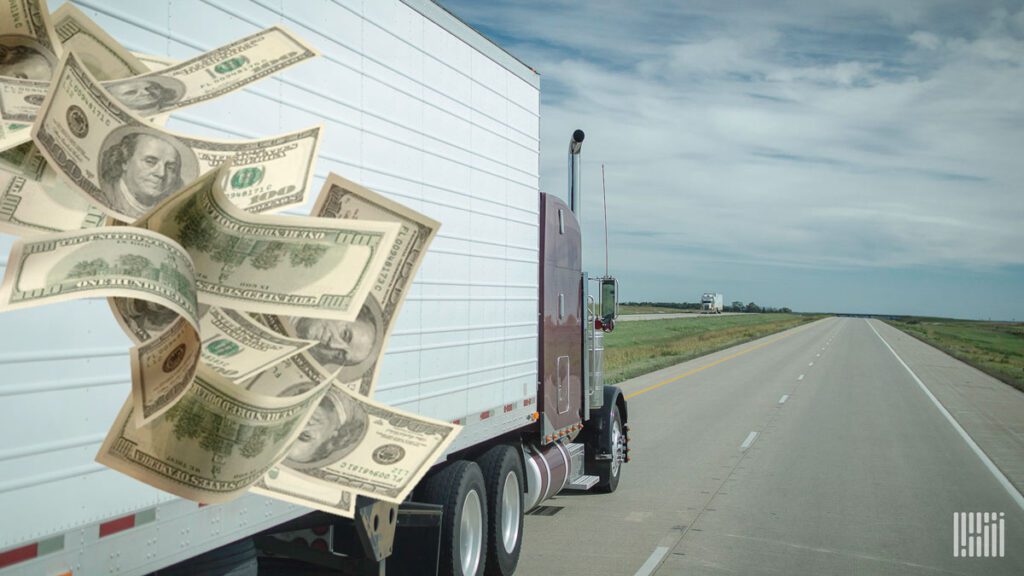
Each department plays a vital role in improving the bottom line
The miles may be long in trucking, but the grind also occurs at a more granular level.
“Trucking is a business of ‘a little goes a long way,’” notes Reliance Partners Director of Safety Robert Kaferle. Everything from contracts to fuel charges and driver pay can be drastically affected by just a nickel or dime, more or less.
A couple of cents more doesn’t sound like much, but at the end of each quarter your accountant can prove otherwise.
“Fuel is getting more expensive and we’re seeing less demand for transportation,” Kaferle said, adding that inflation is also to blame for higher truck, maintenance and payroll costs.
In times like these, the solution isn’t to work harder but smarter. It involves each department working alongside the carrier’s safety program to ensure that the driver’s trip is as efficient, profitable and error-free as possible.
“The best way to save money from an organizational standpoint is by running a comprehensive safety program that addresses the company as a whole,” Kaferle said. “It’s got to involve all departments pulling together for the driver, making sure they’re operational and productive, and that their time is used wisely.”
He said that most organizations fail to see how each department can work alongside its comprehensive safety program to ultimately provide game-changing microsavings.
Take the maintenance department. Though not in charge of operational decisions, its quality of work definitely shows up on the company’s balance sheet.
It’s vital to know whether your scheduled maintenance or preventive maintenance routines are helping or hindering your operation. Consider the wear and tear of the brakes, tires, engine etc. Are your mechanics capable of fixing problems before they become worse?
“Does your maintenance team collaborate with your safety department to create a comprehensive program that addresses the maintenance violations that your drivers face on the road?” Kaferle asked.
Detention is another cash drain. It is perhaps the most painful way to lose money as there’s no way of anticipating it nor is there any way of speeding things up when it occurs.
“Sitting at a dock is unproductive for your drivers and equipment, and it’s actually costing you money,” Kaferle said.
He suggests fleets review their lanes to see where most hang-ups occur. Once they identify the troublesome customer(s), Kaferle said they should not be afraid to constructively address concerns with them.
“Don’t hesitate to work with your customers to increase productivity,” Kaferle said. “Don’t call them and say, ‘Hey, my drivers are being detained and I need to get this fixed.’ Document it, share the data with your customer and explain why it’s an issue.”
But the best way to get to the bottom of what’s really costing your fleet is to simply ask the drivers themselves. Who knows the ins and outs of your operation better than the ones driving from Points A to B and everywhere in between?
“Your drivers know where they’re being detained and the small things that are keeping them from being the most productive,” Kaferle said.
Holding a town hall discussion may be difficult due to the transient nature of the job, but drivers can voice their opinions easily with a poll or questionnaire.
Allowing anonymity encourages drivers to be open and honest, permitting them to point out flaws in the way things are managed. It could even be the safety program itself that’s failing to increase productivity and decrease downtime.
If that’s the case, Reliance Partners is here to help. Kaferle and the Safety Management Team are skilled in building robust safety departments, and with many years of experience, they know a thing or two about maintenance and operations.
“If there is any aspect of your company that you need help with, or if you just want some feedback, we’re always glad to talk,” Kaferle said.